A Comprehensive Guide to the Process and Benefits of Plastic Extrusion
In the vast world of production, plastic extrusion emerges as a very efficient and essential process. Altering raw plastic into continual profiles, it provides to a plethora of industries with its remarkable convenience.
Recognizing the Fundamentals of Plastic Extrusion
While it might appear facility at very first glimpse, the procedure of plastic extrusion is basically straightforward. The procedure begins with the feeding of plastic material, in the type of powders, pellets, or granules, right into a heated barrel. The shaped plastic is then cooled down, strengthened, and reduced into preferred sizes, finishing the process.
The Technical Process of Plastic Extrusion Explained
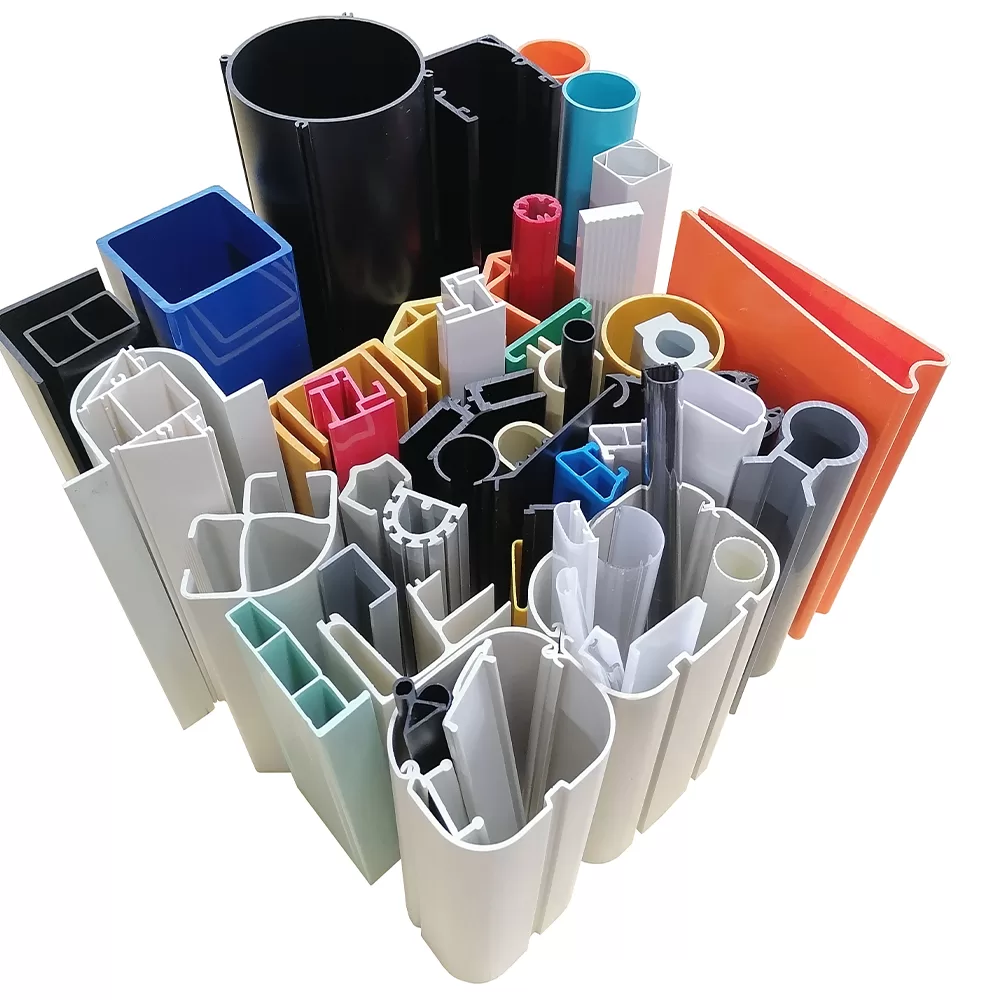
Types of Plastic Suitable for Extrusion
The option of the best kind of plastic is an important aspect of the extrusion process. Different plastics supply one-of-a-kind buildings, making them more fit to specific applications. Understanding these plastic kinds can dramatically enhance the extrusion procedure.
Comparing Plastic Extrusion to Various Other Plastic Forming Techniques
Recognizing the sorts of plastic suitable for extrusion leads the way for a wider conversation on exactly how plastic extrusion piles up versus other plastic forming techniques. These consist of injection molding, strike molding, and thermoforming. Each approach has its special usages and benefits. Shot molding, for example, is superb for creating detailed components, while strike molding is ideal for hollow items like bottles. Thermoforming excels at creating superficial or large components. Plastic extrusion is unparalleled when it comes to developing continuous profiles, such as pipes, seals, and gaskets. It also enables for a consistent cross-section along the length of the item. Thus, the selection of technique mainly depends upon the end-product demands and specifications.
Key Benefits of Plastic Extrusion in Production
In the world of production, plastic extrusion offers lots of substantial benefits. One remarkable advantage is the cost-effectiveness of the process, that makes it an economically appealing manufacturing method. In addition, this method offers exceptional product flexibility and boosted production speed, thereby increasing total production efficiency.
Affordable Production Method
Plastic extrusion jumps to the leading edge as a cost-efficient manufacturing technique in manufacturing. This process attracts attention for its ability to generate high quantities of material promptly and successfully, giving manufacturers with substantial financial savings. The main price advantage is the capability to make use of much less costly resources. Extrusion uses polycarbonate materials, which are less costly contrasted to steels or ceramics. Even more, the extrusion procedure itself is reasonably basic, decreasing labor expenses. In addition, plastic pop over to these guys extrusion needs much less power than conventional production techniques, adding to reduced functional expenses. The process also minimizes waste, as any type of excess or malfunctioning materials can be recycled and recycled, supplying an additional layer of like it cost-effectiveness. On the whole, the financial advantages make plastic extrusion an extremely eye-catching choice in the manufacturing sector.

Superior Item Adaptability
Beyond the cost-effectiveness of plastic extrusion, one more substantial advantage in making lies in its premium item versatility. This makes plastic extrusion a suitable option for sectors that call for personalized plastic elements, such as automotive, construction, and packaging. In essence, plastic extrusion's item adaptability cultivates development while enhancing functional efficiency.
Improved Manufacturing Rate
A considerable advantage of plastic extrusion hinges on its boosted manufacturing speed. This production procedure permits high-volume manufacturing in a fairly brief time period. It can generating long, continual plastic accounts, which significantly lowers the manufacturing time. This high-speed production is specifically useful in industries review where large quantities of plastic components are required within limited target dates. Few various other production procedures can match the rate of plastic extrusion. Furthermore, the capability to maintain constant high-speed manufacturing without sacrificing item top quality establishes plastic extrusion apart from various other techniques. The improved manufacturing speed, for that reason, not only allows manufacturers to fulfill high-demand orders yet additionally contributes to enhanced performance and cost-effectiveness. This beneficial function of plastic extrusion has made it a preferred choice in various industries.
Real-world Applications and Influences of Plastic Extrusion
In the world of manufacturing, the strategy of plastic extrusion holds profound significance. The economic advantage of plastic extrusion, mainly its high-volume and affordable output, has actually reinvented manufacturing. The market is persistently striving for advancements in recyclable and eco-friendly products, showing a future where the advantages of plastic extrusion can be retained without endangering ecological sustainability.
Verdict
Finally, plastic extrusion is a efficient and extremely effective technique of transforming raw products into varied products. It provides various benefits over various other plastic creating techniques, including cost-effectiveness, high outcome, marginal waste, and design flexibility. Its impact is greatly really felt in different industries such as building, automobile, and durable goods, making it a critical procedure in today's manufacturing landscape.
Digging deeper right into the technical procedure of plastic extrusion, it begins with the choice of the proper plastic material. Once cooled, the plastic is cut right into the called for lengths or injury onto reels if the item is a plastic film or sheet - plastic extrusion. Comparing Plastic Extrusion to Other Plastic Forming Methods
Recognizing the types of plastic appropriate for extrusion paves the way for a wider conversation on just how plastic extrusion stacks up against various other plastic creating approaches. Few various other manufacturing procedures can match the rate of plastic extrusion.